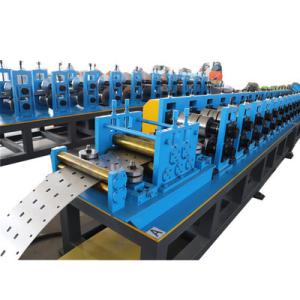
Add to Cart
Shelf System Steel Upright Rack Making Machine
:Shelf uprights are crucial for the safety and efficiency of a detachable shelf system. They are made of cold-formed punching thin-walled steel and have a residual processing stress. The design and selection of uprights are essential for the overall shelf system’s safety and eff iciency The assembly of shelves consists of basic parts like uprights, beams, and optional accessories. The shelf upright’s stability is influenced by the physical properties of the materials used, mold design, and manufacturing accuracy.
The Shelf System Steel Upright Rack Making Machine is built with cutting-edge technology to ensure precision and accuracy during the roll forming process. With constant precision and great efficiency, cut sheet metal into diverse profiles. The feeding and straightening units, roll forming stations, punching and cutting systems, and control systems are all included in the Upright Roll Forming Machine.
The required profile drawing: material thickness 2.0 to 2.5mm
About the punching part: better you can give me the exactly design you like.
The work flow for upright rack forming machine
Shelf System Steel Upright Rack Making Machine
Packing list-upright rack forming machine
No. | Name | Unit | Quantity | Remark |
Part 1 | 5T decoiler with Leveling device | set | 1 | Automatic |
Part 2 | Punching machine with die | set | 1 | |
Part 3 | Main roll former with cutter | set | 1 | |
Part 4 | PLC control station | set | 1 | Chain drive |
Part 5 | Hydraulic oil pump Tracking cutting system | set | 1 | Delta brand |
Part 6 | Product collect table | set | 1 | 6m length |
Decoiler with the leveling machine
Work type | Auto type | |||||||
Loading capacity | 3 Tons | |||||||
Coil inner diameter | 450-550 mm (adjustable) | |||||||
|
Punching machine punch(Yangli Brand )
Working power | 110 tons |
Hole punch quantity | 8 holes one time |
Work speed | 60 times per minute |
Feeder | Servo feeder |
Punch die | Three sets |
About the punching mold design:
1 set combined mold can be used for 3 sets of sizes. By adjust the mold in and out with handrail.
This price contains one working and one spare part
Roll forming system
Rolling shaft material | 40Cr | |
Shaft diameter | 80 mm | |
Roller material | Cr12 HRC 56-58 | |
Rolling station | 18 stations | |
Work speed | 0-20m/min | |
Machine frame | Iron casting vertical structure 35 to 45mm, and another middle plate Each layer 20mm middle plate. | |
Machine body | steel plate welded with grinding | |
Motor brand | Siemens | |
Work power | 22 kw (two motors driving) and two Linear motors | |
Transmission | chain | |
Leveling station | 5 shafts with lost of shaping rollers | |
Straightening | 4 vertical rollers | |
Single side by gear transmission and with two servo motor for size changing: | ||
Whole long shaft, the machine frame will be moved according to the PLC set size. Whole frame will be move on the shaft. |
PLC control system
Frequency brand | Siemens (original) | |
PLC brand | Siemens (original) | |
Screen type | Touch screen & buttons | |
Screen language | English/Chinese/ or other languages | |
Cut command | Yes | |
Profile length set-up | Yes | |
Batch quantity program | Yes |
Hydraulic Servo cutting system
Hydraulic system brand | YUKEN standard (made in China) | |
Work type | Hydraulic running cutting | |
Driving method | By pillar type Cylinder | |
Hydraulic motor power | 5.5 kw | |
Cutter material | GB-Cr12 | |
Cutting length tolerance | ±1mm/3m | |
Cutting feature | Low sounds and steady work condition |
Product collect table
Length | 6 meters |
Width | 0.5 meter |
Work type | Pneumatic |
How to change the cutting blade for different sizes?
For different sizes, please change the cutting blades here.